- Time : Monday-Friday 09am-6pm
- Ceritified ( ISO 9001:2008 )
0982 0944 724 Quick CalL
Our Product Range
the leading stockiest, importers, exporters & suppliers of Alloy 20 Plates
- Home
- Products
- High Nickel Alloys Plates
- Alloy 20 Plates
Alloy 20 Plates
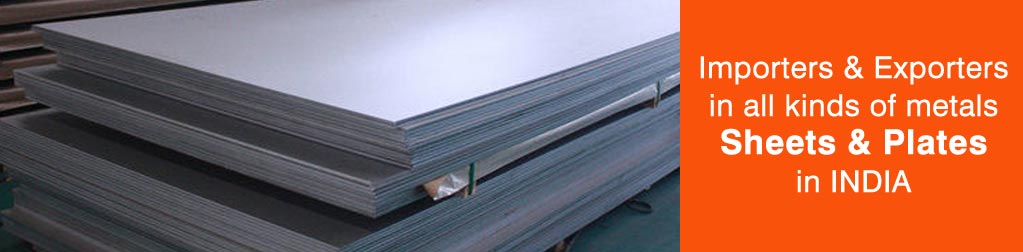
Alloy 20 plates or alloy 20 was designed in particular to face up to sulfuric acid. Its nickel, chromium, molybdenum and copper tiers all offer remarkable trendy corrosion resistance. Confined carbon plus columbium stabilization allows welded fabrications for use in corrosive environments, typically without put up-weld heat treatment. At 33% nickel, alloy 20 has practical immunity to chloride strain corrosion cracking. This alloy is often selected to solve SCC issues, which might also arise with 316L stainless.
Chemistry
Ni | Cr | Mo | Mn | Cu | Si | C | S | P | Cb+Ta | Fe | |
MIN | 32.5 | 19.0 | 2.0 | - | 3.0 | - | - | - | - | 8.0 x C 1.0 | - |
MAX | 35.0 | 21.0 | 3.0 | 2.0 | 4.0 | 1.0 | 0.06 | 0.035 | 0.035 | - | Balance |
Specifications
o ASME SA 240, ASME SB 366, ASME SB 463
o ASTM A 240, ASTM B 366
o ASTM B 463
o ASTM B 473
o EN 2.4660
o UNS N08020
o Werkstoff 2.4660
o ASTM A 240, ASTM B 366
o ASTM B 463
o ASTM B 473
o EN 2.4660
o UNS N08020
o Werkstoff 2.4660
Inventory
Alloy 20 Coil, Alloy 20 Plate, Alloy 20 Sheet, Alloy 20 Weld Wire Supplier and exporters.
Common Trade Names
Carpenter® 20, 20CB-3®
Features
• Excellent resistance to hot sulfuric acid
• Resistant to intergranular corrosion in the as-welded condition
• Chloride stress corrosion cracking resistance
• Resistant to intergranular corrosion in the as-welded condition
• Chloride stress corrosion cracking resistance
Applications
• Sulfuric acid pickling tanks, racks and heating coils
• Phosphate coating drums and racks
• Heat exchangers
• Bubble caps
• Process piping
• Mixing tanks
• Chemical and petroleum process equipment
• Phosphate coating drums and racks
• Heat exchangers
• Bubble caps
• Process piping
• Mixing tanks
• Chemical and petroleum process equipment
Physical Properties
Density: 0.278 lb/in3 annealed
Melting Point: 2525-2630°F
Electrical Resistivity: 651 Ohm-circ mil/ft
Melting Point: 2525-2630°F
Electrical Resistivity: 651 Ohm-circ mil/ft
Temperature, °F | 70 | 212 | 392 | 572 | 752 | 842 | 932 |
Coefficient* of Thermal Expansion, in/in°F x 10-6 | - | 8.16 | 8.37 | 8.62 | 8.62 | 8.84 | 8.91 |
Thermal Conductivity Btu • ft/ft2 • hr • °F |
6.7 | 7.57 | 8.56 | 9.53 | 10.5 | - | - |
Modulus of Elasticity, Dynamic psi x 106 | 28 | - | - | - | - | - | - |
* 70°F to indicated temperature
Mechanical Properties
Minimum Specified Properties, Asme Sb-688 Plate
Ultimate tensile strength, ksi | 80 |
0.2% yield strength, ksi | 35 |
Elongation, % | 30 |
Hardness MAX, Brinell | 217 |
Typical Tensile Properties, Bar
Temperature, °F | 70 |
Ultimate Tensile Strength, ksi | 91 |
0.2% Yield Strength, ksi | 48 |
Elongation, % | 45 |
Charpy Impact V-notch, ft-lbs | 200 |